Recycled plastics deliver revolutionary results in moulds for virgin plastic
- miapersson
- Nov 21, 2024
- 4 min read
Updated: Nov 22, 2024
High-quality recycled-based plastic materials performs equivalently to virgin-based materials in moulding tools designed for virgin plastics. This is the experience of Polykemi’s customer Simoldes Plastics, a supplier to Stellantis, VW Group, the Renault-Nissan-Mitsubishi alliance, BMW, Toyota, Scania and Mercedes-Benz. Tests and evaluations have also shown recycled materials to have surprising properties that may revolutionize our perception of recycled plastics.

Frame for interior door handle in the material REZYcom PC/ABS R85H UV Satin Black.
Seamless replacement from virgin materials to recycled alternative
It all started as a request from Simoldes Plastics’ customers in the automotive industry to increase the proportion of recycled plastic in their products. This led to a closer collaboration between technical experts at Polykemi and Simoldes Plastics, with extensive testing and evaluation of how plastics based on high-quality recycled raw materials behave in tools previously only used for plastics made from virgin materials. The involved parts in this project were interior door frames and panels and all tests showed that recycled plastics perform extremely well in moulds previously used for virgin materials, without any changes at all.
“All evaluations have shown results above expectations. Our processes work well with engineering thermoplastics based on mechanical recycled content in the way we would expect with virgin materials. With the reliable partners at supply chain, we’re ready to begin serial production”, says Mariusz Nowak, Project Manager Research and Innovation at Simoldes Plastics.
“The ability to use existing moulds and still have end products with equally high quality is a dream outcome in a project such as this. It meant that the transition would not require any major investments in new machines or personnel training for our customer,” says Jörgen Olsson, Technical Manager - Plastic Applications & Processing Specialist at Polykemi.
Simoldes can count on reduced emissions
When production switches and virgin materials are replaced with recycled materials, Simoldes Plastics will be able to show precise emission savings using Polykemi’s expertise and advanced analysis. The key of the reduction lies in making conscious material choices.
“Our initial calculations, with the help of our Materialsmart® concept*, show that Simoldes Plastics will lower its CO₂ emissions by 54-68 % per manufactured part. Which is extremely good news for them, for us and the planet,” says Jörgen Olsson.
“The materials we use during production have a significant impact when it comes to CO₂ emissions. As a leading TIER 1 supplier to European OEM’s, collaborating on this technical case study alongside Polykemi within the Simoldes project BOOST**, is a good starting point to be a reliable partner in reducing emissions within the GRI scopes 1, 2 and 3,” says Mariusz Nowak.
Insert moulded door panel with both textile or foil and the recycled material REPRO ABS RE5.
Recycled materials quality challenges perceptions
The tests also evaluated how recycled materials cope with more complicated processes, such as insert moulding. Results from tests involving ABS injection moulding using recycled materials and either textile or foil in the moulds, were equivalent to those from injection moulding using new materials.
“The ability of recycled materials to cope with such a process is a testimonial to its high quality. Old perceptions that recycled raw materials provide poor results and are more difficult to process can definitely be discarded now,” says Jörgen Olsson.
“This shift in perception of recycled raw materials is vital as the automotive sector move towards incorporating materials with mechanical recycled content to a much greater extent. To optimize the process further, the automotive industry needs a new approach with new guidelines, providing advice on using recycled materials, when creating new specifications. That’s why cooperation is crucial when developing strong technical solutions. We all need to work together!’’ says Mariusz Nowak.

Mariusz Nowak, Project Manager Research & Innovation at Simoldes Plastics, and Jörgen Olsson, Plastic Applications and Processing Specialist at Polykemi.
Driving Sustainability: Circular Approach in Automotive Injection Process
Circular Economy requires a paradigm shift and a fresh perspective within the automotive industry. Embracing the principles of the 5Rs – Rethink, Refuse, Reduce, Reuse, and Recycle – becomes imperative in every facet of the automotive manufacturing process. The injection process, a critical component of automotive manufacturing, is a focal point for implementing these sustainable practices. Shifting towards eco-friendly materials, optimizing resource usage, and integrating recycling strategies into the injection molding process are pivotal steps that aligns with environmental consciousness meeting the demands of a circular economy for a greener future.
“We are in a U-shaped circular economy in the automotive industry, and we need to make the transition to a O-shaped format.” says Mariusz Nowak.
This successful collaboration between Simoldes Plastics and Polykemi has laid a good foundation not only for change in the automotive industry but also for more collaborations between the two companies.
About Polykemi
High-quality plastic compounds based on virgin and recycled raw materials
Ever since its founding in 1968, Polykemi has developed and produced plastic compounds based on both virgin and recycled raw materials. Today, Polykemi’s recycled materials for injection moulding consists of two product groups: REPRO (standard range) and REZYcom (customized range). This means Polykemi’s customers get high-quality compounds based on recycled raw materials that not only save CO₂ emissions, but also have corresponding technical properties as the virgin based products.
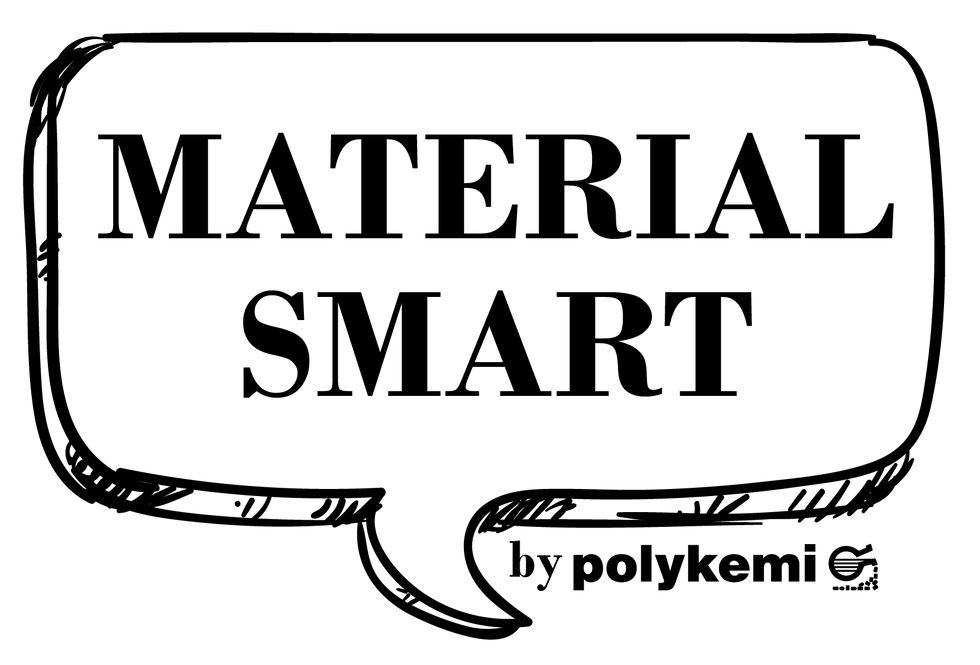
*The Materialsmart® concept means that Polykemi can present the environmental impact for their compounds manufactured in their own worldwide production facilities, which means they can help their customers make the optimal material choice.
Read more at materialsmart.info
About Simoldes
Innovative and sustainable approach to plastic moulding
Simoldes Plastics, a Portugal-based industry leader with 40 years of experience, specializes in high-quality plastic components for the automotive market. Operating internationally across Europe and South America, it features advanced manufacturing facilities ensuring precision and efficiency. Their focus on lightweight, durable solutions aligns with eco-friendly practices, emphasizing recyclable materials and energy efficiency. Through ongoing research and development, Simoldes Plastics provides innovative, customized products, maintaining its position as a trusted partner in the plastics industry.

**Simoldes BOOST project was launched in April 2021 and is one of Simoldes Plastics many sustainability programs. The project aims to increase the amount of recycled materials within the automotive industry.
Read more at Boost - Simoldes or simoldes.com